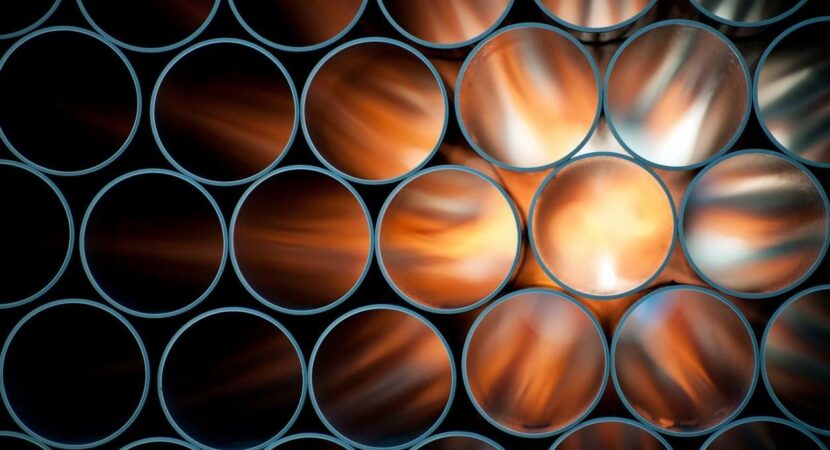
By Germain HURTADO – A sustainable chemistry, called green chemistry, also focuses on the environmental impact of chemistry, including reducing consumption of non-renewable resources and technological approaches to pollution prevention.
Green chemistry addresses our future challenges, working with processes and chemicals, inventing new reactions, preventing chemical pollution and managing resource depletion.
In 2005, Prof. Robert GRUBBS (USA), Dr. Richard SCHROCK (USA) and Dr. Yves CHAUVIN (FR) collectively received the Nobel Prize in Chemistry, thanks to the development of the metathesis method in organic synthesis. While this technology has been widely used in industry for the manufacture of drugs and chemical intermediates, the use of a ruthenium catalyst for Ring Opening Metathesis Polymerization (ROMP) of olefins has enabled the launch of new high performance polymers. The main advantages of ROMP are the saving of atoms, the very low consumption of activation and process energy, as well as the very low production of by-products and hazardous waste. Tick 5 Key Boxes of Green Chemistry Principles
On both sides of the Atlantic, two start-ups, Materia Inc. (Materia Inc.). (Pasadena, CA) and DEMETA SAS (Rennes, France) came up with the idea of utilizing this discovery by formulating scyllo-olefins, including DCPD (dicyclopentadiene), with additives and a catalytic system. By simply mixing, the reaction is initiated and leads to a polymer with unique mechanical and thermal characteristics. It is noted that these catalysts are extremely robust, not sensitive to oxygen or water and therefore do not require complex molds or injection systems. The two start-ups have patented their slightly different systems and market them under the brand names Proxima® and NexTene™, respectively.

The classic cladding families are:

• Polyurethanes that are generally sensitive to high temperatures (> 80° C)
• Epoxies have limited resistance to moisture and are brittle. Also, some formulations can be very expensive.
• Widespread polypropylene is not temperature resistant (both high and low) and injection equipment and tools are quite expensive.
• Silicones have good thermal properties but are expensive for most applications.
Other technical polymers such as PEEK or PVDF are appearing in our industries but they are not widely available and very expensive, both in terms of implementation and CO2 balance.
Unlike these materials, Proxima® and NexTene ™ resins combine excellent resistance to corrosion, hydrolysis, temperature, very good thermal insulation and a density close to 1.
In addition to coatings, such as those used in the Appomattox project in the Gulf of Mexico, the type of resins developed by Demeta and Materia also find applications in the fields of buoyancy modules, customized coatings (combining corrosion protection and excellent thermal insulation) but also in the field of composite materials, allowing, thanks to a density of 1,03, to further reduce the weight of subsea installed systems.
Helps reduce the carbon footprint of projects
“Our product is fully involved in efforts to reduce our industries' carbon footprint. That of NexTene ™ is reduced by half compared to that of epoxy resins, polyurethane, polypropylene, etc… and this without compromise, neither in mechanical properties, nor in thermal properties, nor in its implementation”.
Patrick PIOT, CEO of DEMETA.
Unfortunately, there are countries that blindly trust…
parabéns
Damn, you're cool, right bro?
Answering one of your questions, today…
I think it’s a bit disastrous to baptize…
ERRATA: in some parts the text mentions…
Dude, stop it! South Dakota…
I would like to know how to send your CV