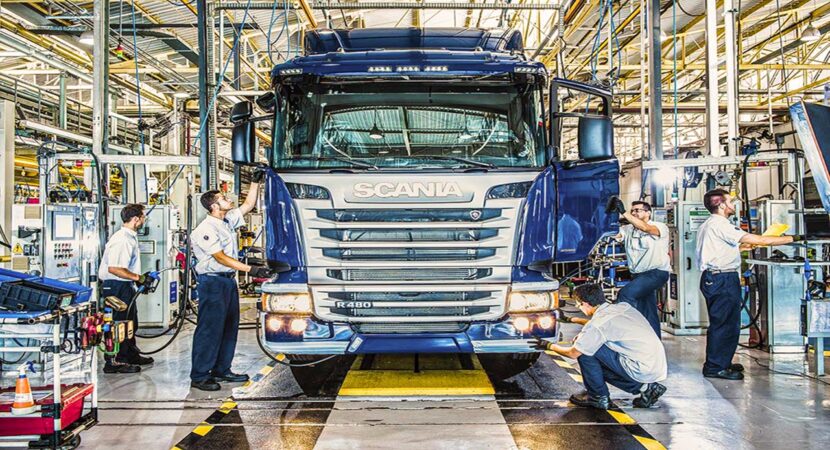
Scania replaces 40 lead-acid battery forklifts with lithium-ion electric forklifts at the São Paulo unit, in defense of the energy transition
Vinhedo (SP) unit of the multinational vehicle manufacturer Scania, which is responsible for the supply of spare parts for Latin America, optimizes operations and has just completed the process of replacing 40 lead-acid battery forklifts with 40 electric forklifts ion batteries and employees gain increased productivity with safety and more ergonomics.
Read also
- With the departure of Ford from Brazil, a former metallurgist at the multinational vehicle manufacturer joins PDV, becomes an entrepreneur and opens a mega paint store in SP with space to train professional painters
- Logistics companies and other segments open enrollment for candidates with no experience looking for their first job in SP; some internship and trainee vacancies are 100% home office (remote), candidates from all over Brazil can participate and salaries reach R$ 6.000!
- Brazil inaugurates an unprecedented technological solution for recycling and energy recovery of urban and industrial waste capable of generating up to 2 MW of energy per ton of waste processed
- By 2025, 85 million jobs will be replaced by the shifting divide between humans and machines, and 97 million new roles are expected to be created in the wake of technological innovations.
The project, which includes leasing handling equipment, installing loaders and implementing the telemetry system, is the result of a partnership with Jungheinrich, one of the global leaders in intralogistics solutions.
Fleet renewal and modernization, Scania guarantees an increase in production and a reduction in polluting gas emissions
With the renewal and modernization of the fleet, Scania guarantees the reduction of polluting gas emissions, as well as energy costs, the optimization of the intralogistics operation through telemetry, the increase of comfort and safety of operators and, consequently, a leap in productivity. The Jungheinrich equipment chosen for the project are vertical order pickers, counterbalanced forklifts, reach trucks, horizontal order pickers and on-board pallet stackers.
“This investment represents the continuous improvement of our processes within the Industry 4.0 concept. In addition to being sustainable, we have a telemetry system that allows us to measure how long the machines are actually used and, thus, identify whether there is a need to increase or reduce the number of pieces of equipment,” explains Giliard Guerreiro de Souza, manager of the Logistic Parts Center (LPC) by Scania Latin America.
Scania has become the world's first commercial vehicle manufacturer to have its climate targets approved by the Science Based Target Initiative (SBTi)
In 2020, Scania became the first commercial vehicle manufacturer in the world to have its climate targets approved by the Science Based Target Initiative (SBTi). Among them is the objective of reducing by 50% the emission of CO2 from its operations around the world. “The replacement of equipment contributes to Scania's goals of reducing emissions globally, but also demonstrates the commitment of operations in Latin America to global warming”, highlights Giliard.
Scania's actions at the LPC, as well as at the plant in São Bernardo do Campo, are mainly dedicated to improving energy efficiency, reducing energy consumption and making the shift to renewable energies.
For Marcela Magnani, Process Analyst who coordinated the implementation of the project at LPC, there are a series of gains and benefits that the new forklifts bring to internal and safety processes. “Easy and quick loading of the machine increases equipment availability. Collaborators can upload it during break times, such as their lunch break”, she explains. Marcela also highlights the importance of the new equipment for the well-being of the operators: “We gained in ergonomics, taking into account that it is possible to make personalized adjustments for each employee, in addition to other additional functions that focus entirely on the operator”, she concludes.
According to Raphael Souza, Jungheinrich's Commercial Corporate Manager, telemetry is a powerful ally for fleet management, allowing in-depth analysis of the operational profile of each piece of equipment. “It identifies whether or not a particular forklift is fulfilling its primary logistical function, as well as providing a view on the dispersion of use over days and hours, analyzing the driving behavior of operators and identifying impacts”, highlights the executive. “It also brings features such as check-lists, which expand the fleet's productive potential and make it safer for employees”, emphasizes Souza.
The technology also allows the creation of “virtual fences”. Thus, if any machine circulates in an inappropriate location, the system will send a notice to the person in charge with the alert. Jungheinrich equipment also parameterize different profiles for different users, allowing only operators qualified for certain equipment to operate them.
Innovative technology to the efficiency and sustainability of lithium brings excellence to the operation and relevant cost reduction
SUSTAINABILITY – The addition of this innovative technology to the efficiency and sustainability of lithium brings excellence to the operation and significant cost reduction. High performance, recharges in just a few minutes, zero battery maintenance and long machine life guarantee the constant availability of these equipment in three shifts, with no gas emissions, no risk of acid spillage, no risk of accidents with operators during changeovers battery, nor the need for battery rooms – as in the case of lead-acid technology – or even battery backup. “With these changes, we foresee significant gains for the process and for the environment. Energy savings alone should reach 30%,” says Souza.
At the end of the lithium battery's life cycle, Jungheinrich takes care of the entire disposal process to avoid any kind of damage to the environment. To this end, the company guarantees them a second life, as stationary batteries, even serving as reservoirs for solar and/or wind energy, or promotes their correct disposal for recycling, through accredited companies qualified to deal with this type of waste. residue.
“Consumer awareness has gained a new perspective. Companies are increasingly concerned about ensuring the so-called ESG (Environmental, Social and Governance) standard. In practice, the company must be consistent throughout its process to be considered sustainable. Thus, it is essential that this whole part of intralogistics be reviewed. Consumers will charge all companies for this, it's a matter of time”, emphasizes the Jungheinrich executive.
Middle and higher education job openings to work at Scania's SP factory
Those interested in building a career at the multinational Scania — world leader in the production of heavy trucks, buses and industrial and marine engines, should register their CV, directly on the company's website at this link. Check out in the video below how Scania's production line works!